Traditional Method
Traditionally, BGA reballing relies on a manual approach, utilizing microscopes and precision tools to carefully de-tin, clean, and re-tin components. This work requires significant skill from the operator, leaving room for inconsistencies and defects that can impact component reliability.
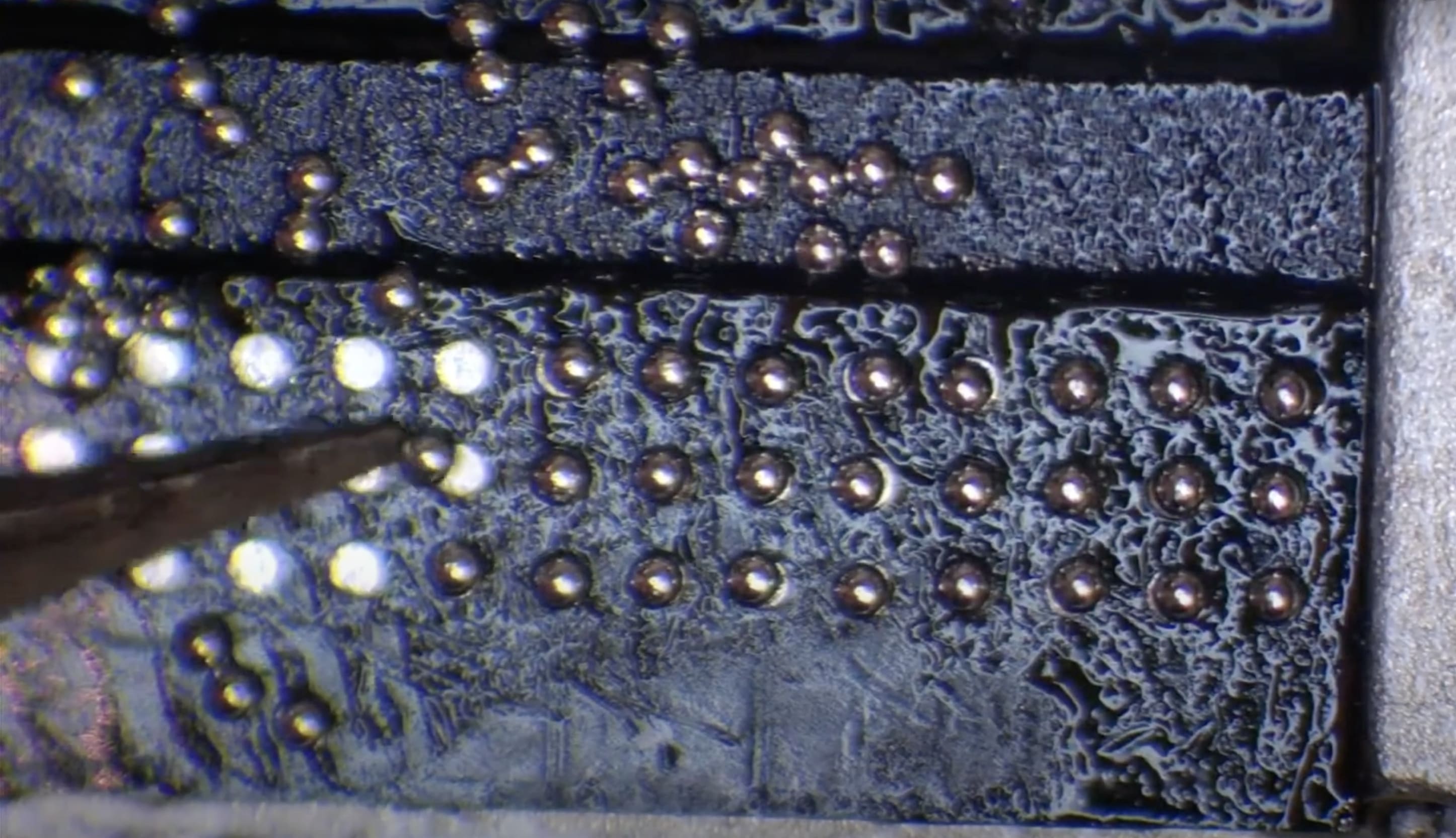
New Method
Our BGA reballing machine provides an end-to-end solution for the reballing workflow. This system is capable of executing the entire process, from tin removal to final inspection, and can accommodate most BGA components (0.3mm – 0.76mm). By automating this process, the reballing of components can be performed with unparalleled speed, precision, and consistency.
The ZQ3500 enables users to perform BGA rework operations faster, cheaper, and more precisely than ever before.
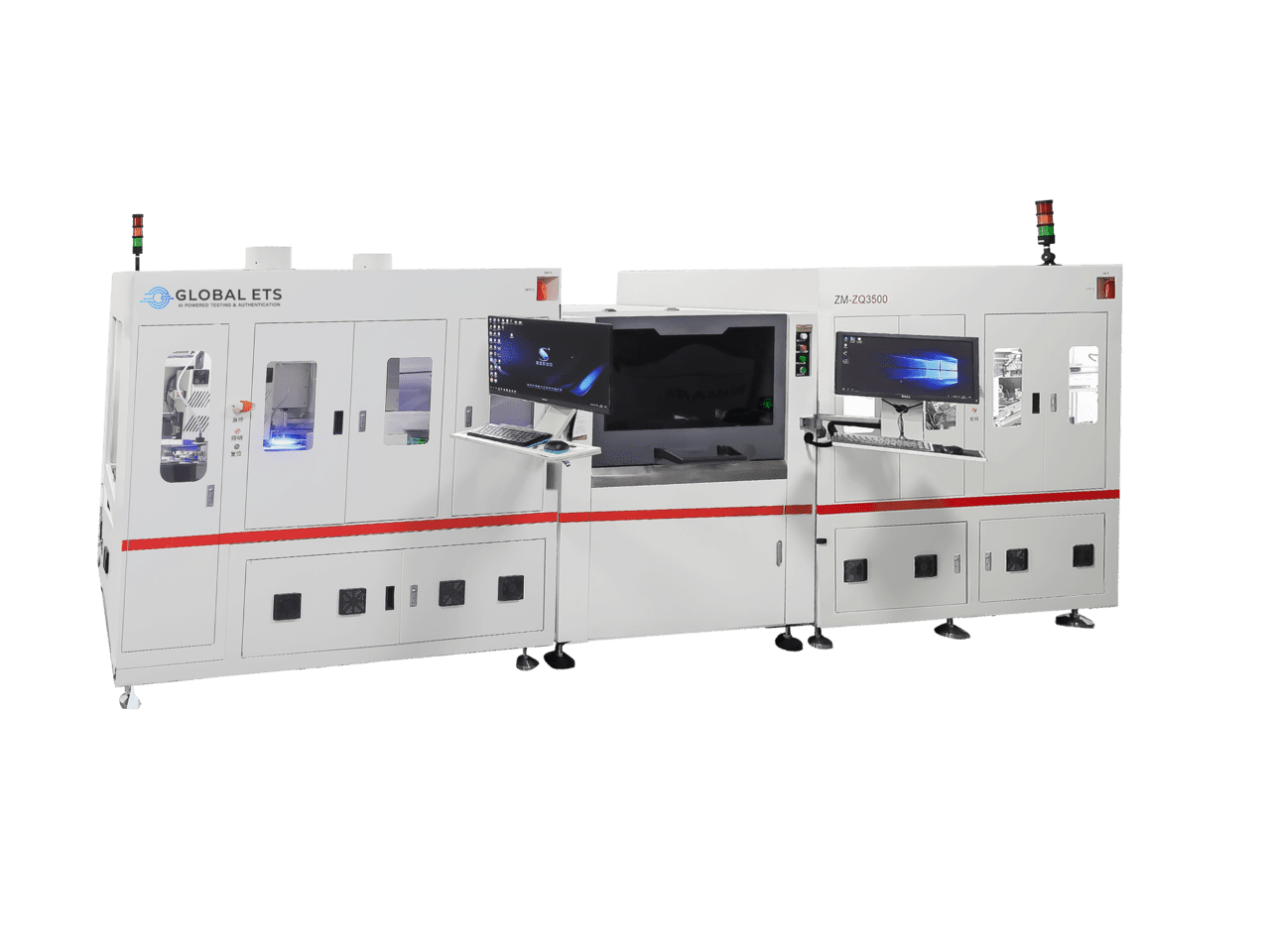
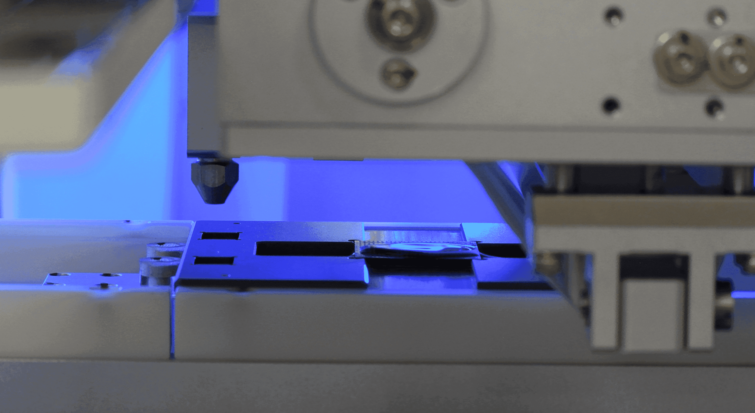
Tin Removal & Cleaning
The ZQ3500’s multi-functional tin removal system combines preheating, non-contact suction, hot air heating, and high-temperature scraping to remove solder balls and residue from BGA components. This is followed by a high-speed polishing and cleaning process to prepare the surface.
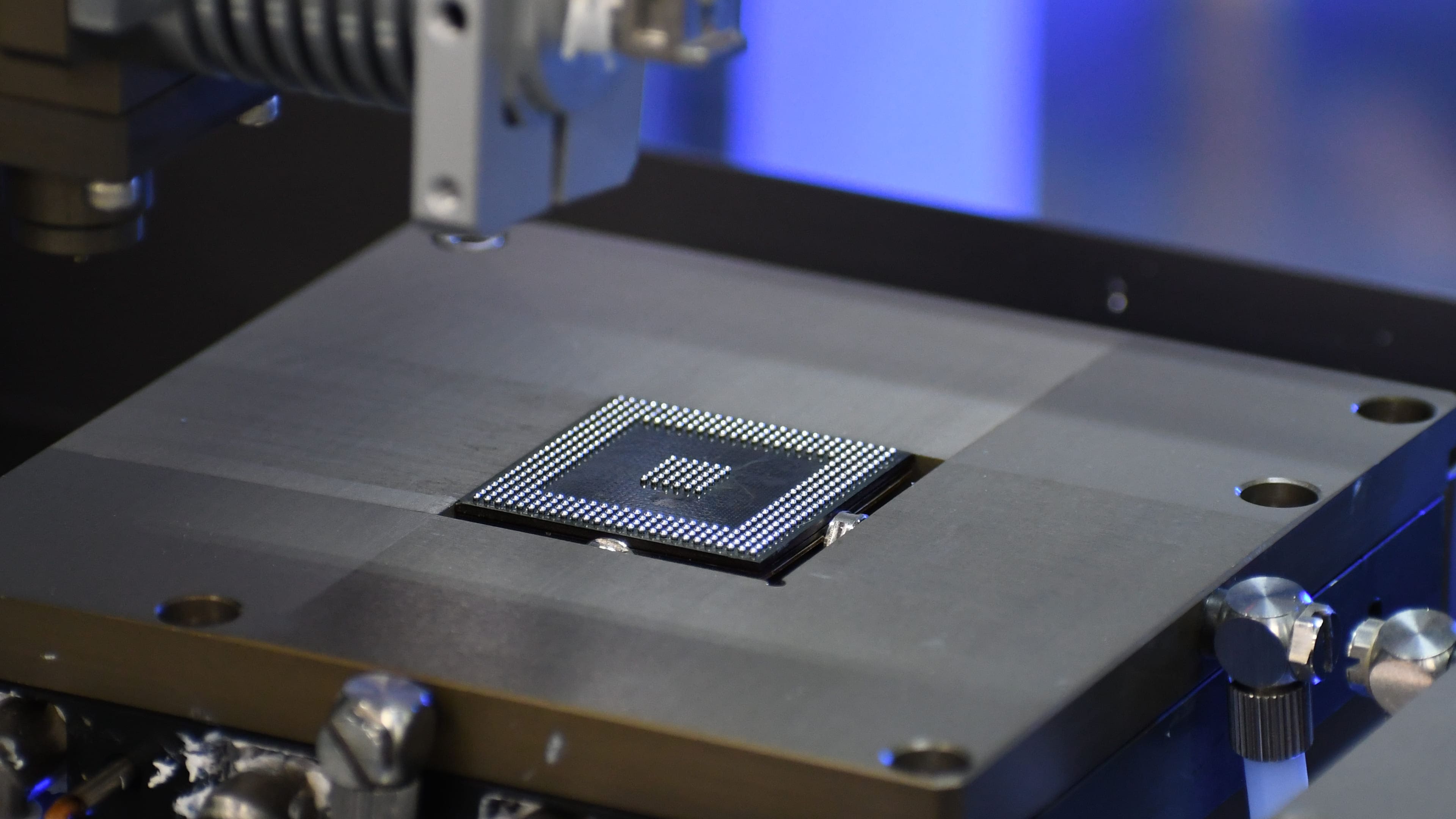
Flux Application & Reballing
Following cleaning, our machine can automatically print flux onto the BGA or apply it via a high-speed spot dispenser, depending on the component type. It then precisely aligns and attaches the new solder balls, ensuring consistent quality.
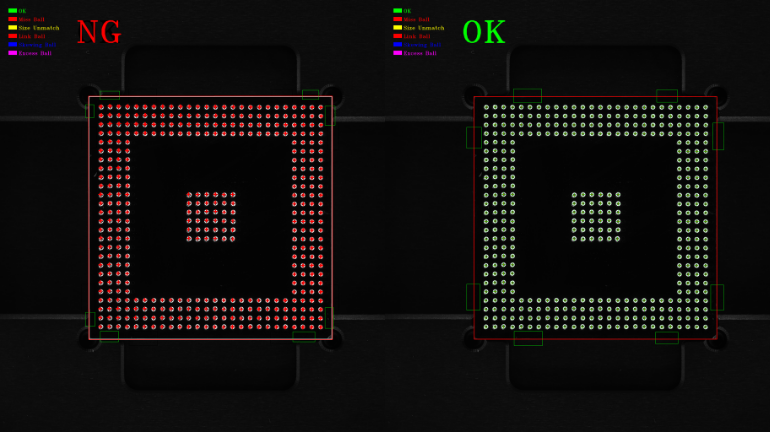
Inspection & Sorting
Integrated with CCD positioning and AOI detection systems, the ZQ3500 will perform comprehensive inspections, identifying any defects that may be present. Having these systems also allows the machine to sort the BGAs, ensuring only fully reworked and functional components are passed.